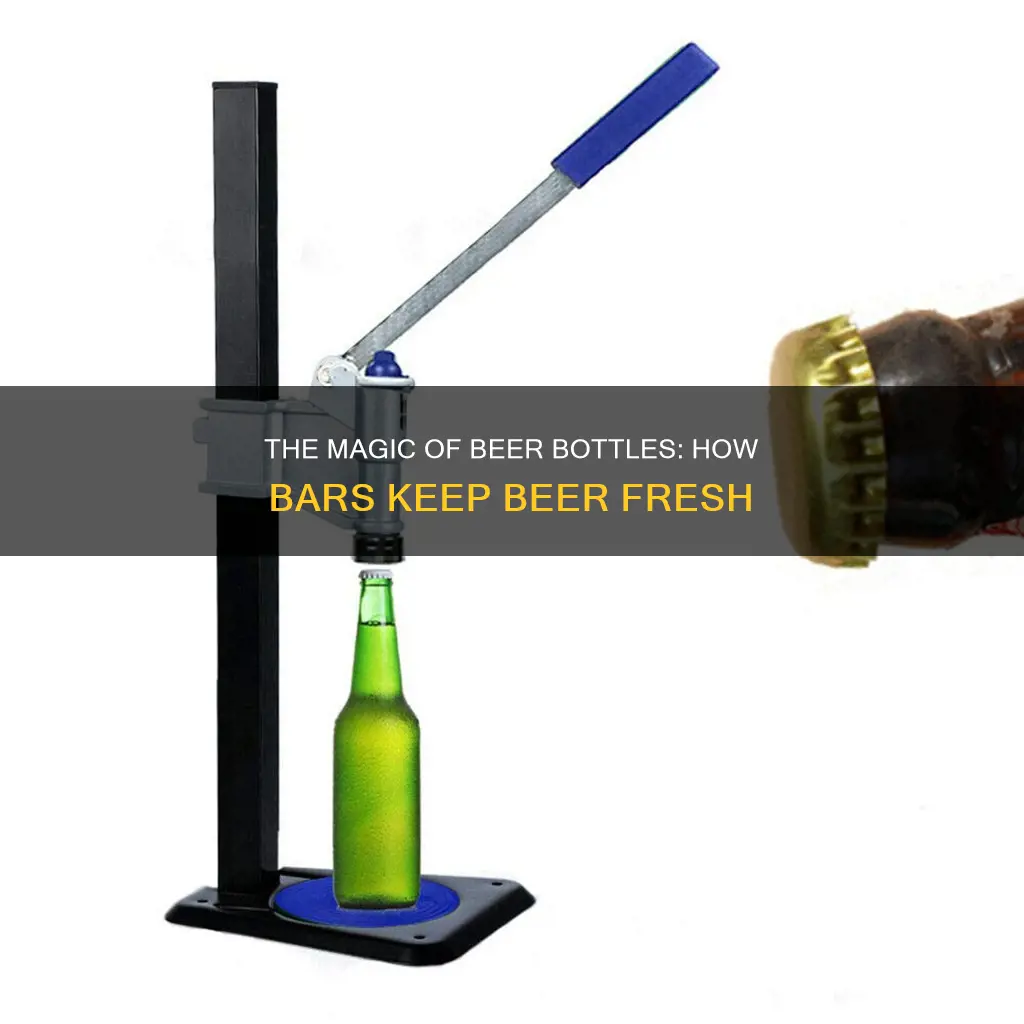
What bars put beer in and seal them? The answer lies in the fascinating world of beer packaging and distribution. Beer bottles and cans are typically filled and sealed at breweries or specialized filling stations, where the beer is carefully poured into containers and then sealed with a cap or lid. These sealed containers are then distributed to bars, restaurants, and other retailers for sale and consumption. The process of filling and sealing ensures that the beer remains fresh and flavorful until it reaches the consumer.
What You'll Learn
- Materials: Glass, metal, plastic, and ceramic are common beer bottle and can materials
- Cap Types: Crown caps, pull-tabs, corks, and screw caps are used for sealing
- Brewing Process: Beer is carbonated and sealed during the brewing process
- Distribution: Bottling and canning lines automate the sealing process in breweries
- Consumer Experience: Proper sealing ensures beer freshness and taste
Materials: Glass, metal, plastic, and ceramic are common beer bottle and can materials
Glass, metal, plastic, and ceramic are the primary materials used for beer bottles and cans, each offering unique advantages and characteristics. Glass bottles have been the traditional choice for centuries due to their ability to enhance the beer's flavor and appearance. They are known for their clarity, allowing customers to see the beer's color and carbonation, which is essential for a visually appealing presentation. Glass is also inert, meaning it doesn't react with the beer, ensuring the beverage's taste remains pure and unadulterated. However, glass bottles can be heavy and fragile, making them less ideal for transportation and potentially increasing the risk of breakage.
Metal cans, on the other hand, have gained popularity for their lightweight and durable nature. They are often used for canned beer due to their ability to maintain the beer's freshness and prevent light exposure, which can cause flavor degradation. Metal cans are also stackable, making them efficient for storage and transportation. The material's inertness ensures that the beer's taste is not altered, and the can's design often includes a pull-tab or a pop-top, providing a convenient and fun drinking experience.
Plastic bottles have become increasingly common, especially for craft and specialty beers. Plastic is lightweight, making it easier to transport and less prone to breakage, which is a significant advantage over glass. Additionally, plastic bottles can be designed with various colors and shapes, allowing for creative branding and marketing. However, some beer enthusiasts argue that plastic may not provide the same level of flavor preservation as glass, and its durability might not match the longevity of glass bottles.
Ceramic bottles, though less common, offer a unique and traditional approach to beer packaging. Ceramic is known for its ability to insulate, keeping the beer cool and fresh. These bottles often feature intricate designs and can be customized with various colors and patterns. While ceramic bottles might be heavier and more fragile than glass, they provide an eco-friendly alternative, as they are reusable and can be recycled, reducing the environmental impact of beer packaging.
In summary, the choice of material for beer bottles and cans depends on various factors, including the desired presentation, taste preservation, convenience, and environmental considerations. Each material offers distinct advantages, and bars often select these materials based on their specific needs and the beer's characteristics they want to showcase. Understanding these materials and their properties is essential for creating an enjoyable and memorable beer-drinking experience.
Brewed Adventure: A Guide to Stuffing Beer in Turkey
You may want to see also
Cap Types: Crown caps, pull-tabs, corks, and screw caps are used for sealing
The world of beer packaging employs various cap types to ensure the beverage remains fresh and sealed until the moment of consumption. These caps are designed to provide an airtight barrier, preventing the entry of oxygen and other contaminants that could compromise the beer's taste and quality. Here's an overview of the common cap types used for sealing beer bottles and cans:
Crown Caps: These are the classic, iconic caps that have been used for decades. Crown caps, also known as crown corks, are made of aluminum and feature a distinctive crown-like design. They are widely recognized for their ability to provide an effective seal. The process involves a two-piece system: the cork and the crown. The cork is inserted into the bottle or can, and then the crown is crimped onto it, creating a tight seal. This type of cap is commonly used for canned beers and is known for its durability and ease of opening.
Pull-Tabs: Pull-tabs are a unique and innovative sealing mechanism, especially popular in the United States. These caps are typically made of aluminum and are designed with a small tab that can be pulled to open the container. The tab is connected to the can's interior, and when pulled, it tears open the can, allowing access to the beer. This method provides a convenient and mess-free way to open cans, making it a favorite among many beer enthusiasts.
Corks: Corks are a traditional and elegant choice for sealing wine bottles, but they are also used for certain types of beer, particularly craft and specialty beers. These caps are made from natural cork material and are known for their ability to provide an airtight seal. Corks are often used in bottles with a twist-off mechanism, where the cork is inserted and then twisted to open. While less common in the mass-market beer industry, corks offer a premium and sophisticated experience for beer enthusiasts.
Screw Caps: Screw caps, also known as caps or bottle caps, are widely used for both bottles and cans. These caps feature a metal or plastic screw-on mechanism that provides a secure seal. The process involves threading the cap onto the container's neck, ensuring a tight fit. Screw caps are known for their reliability and are commonly used in the production of craft beers, as they offer a consistent and controlled opening experience. They are also easy to recycle and are an environmentally friendly choice.
Each of these cap types serves a specific purpose, catering to different preferences and production methods in the beer industry. Whether it's the classic crown cap, the innovative pull-tab, the traditional cork, or the reliable screw cap, these sealing mechanisms play a crucial role in delivering the perfect beer to the consumer.
Unconventional Hair Care: A Beer-Infused Guide to Shiny Strands
You may want to see also
Brewing Process: Beer is carbonated and sealed during the brewing process
The brewing process is an intricate art that transforms simple ingredients into the beloved beverage known as beer. One crucial aspect of this process is the carbonation and sealing of the beer, which contributes to its unique flavor and refreshing quality. This step is often overlooked by beer enthusiasts, but it plays a vital role in the overall drinking experience.
Carbonation is introduced to beer during the fermentation stage. When yeast ferments the sugars derived from malted grains, it produces alcohol and carbon dioxide (CO2) as byproducts. This CO2 is what gives beer its fizz and makes it sparkle. The fermentation vessel, often a large steel tank, is crucial here. It needs to be kept under pressure to allow the CO2 to dissolve into the beer. This process can take several weeks, and the duration depends on the style of beer being brewed. For example, lagers typically ferment at lower temperatures and take longer to carbonate compared to ales.
After fermentation, the beer is transferred to another vessel for conditioning. During this stage, the beer is aged, and the flavors mature. It is also during this period that the beer is carbonated further. The beer is often kept at a slightly higher pressure, allowing more CO2 to dissolve into the liquid. This step is crucial as it contributes to the beer's overall taste and mouthfeel. The longer the beer is conditioned, the more carbonated it becomes, resulting in a more intense and satisfying drinking experience.
Sealing the beer is an art in itself. Once the beer has been conditioned and carbonated to the desired level, it is time to package it. The most common method is using a process called 'canning'. This involves filling the beer into cans, which are then sealed with a two-piece lid. The lid has a pull-tab, which, when pulled, tears open the lid, allowing the beer to be poured. This method ensures that the beer remains carbonated and fresh until the consumer opens the can.
Another popular sealing method is bottling. Beer is filled into bottles, which are then sealed with a cork and cap. The cork is typically made of natural materials like cork oak and is designed to allow some CO2 to escape, creating a natural carbonation. This method has been used for centuries and is still prevalent in craft breweries. The sealing process must be precise to ensure the beer's quality and to prevent any contamination.
In summary, the brewing process of beer involves a careful and intricate dance of carbonation and sealing. From the fermentation stage to the final packaging, each step contributes to the beer's unique character. The carbonation adds that refreshing fizz, while the sealing process ensures the beer remains fresh and flavorful until it reaches the eager consumer. Understanding these processes can enhance one's appreciation of the diverse world of beer.
Brewing at Home: Exploring the Beer-Crock Pot Combo
You may want to see also
Distribution: Bottling and canning lines automate the sealing process in breweries
The process of sealing beer bottles and cans is a crucial step in the distribution and sale of beverages, and breweries have long relied on specialized equipment to automate this task. Bottling and canning lines are designed to streamline the production process, ensuring that each container is filled, sealed, and ready for distribution efficiently. These machines are an integral part of modern brewing operations, allowing breweries to meet the high demand for their products while maintaining quality and consistency.
Bottling lines are typically used for smaller batches or craft breweries that produce a variety of beer styles. The process begins with a conveyor belt that transports empty bottles or bottles with pre-added labels to the filling station. Here, a precise mechanism measures and dispenses the appropriate amount of beer into each container. This step requires accuracy to ensure the correct volume and carbonation level. After filling, the bottles are sealed using a corking or capping machine. Corking machines are often used for premium or traditional beer styles, while capping machines are more common for lagers and pilsners. These machines insert a cork or screw cap into the bottle's neck, ensuring an airtight seal. The sealed bottles then move along the line, where they are labeled, dated, and packed into cases or crates for shipping.
Canning lines are designed for larger-scale production and are particularly useful for breweries that produce canned beer, often associated with convenience and portability. The canning process starts with a similar conveyor system, but instead of bottles, it carries aluminum cans. The filling process is similar to bottling, with precise measurements to ensure the correct beer volume. After filling, the cans are sealed using a sealing machine. These machines use a combination of heat and pressure to create a hermetic seal, ensuring the beer's freshness and preventing any contamination. The sealed cans are then labeled, often with a unique code or batch number, and packed into cases for distribution.
The automation provided by these bottling and canning lines offers numerous advantages. Firstly, it significantly increases production speed and efficiency. Machines can process a large number of containers per hour, reducing the time required to fill, seal, and package beer. This automation also minimizes the risk of human error, ensuring consistent quality across all batches. Additionally, these lines can be programmed to adapt to different beer styles and container sizes, providing flexibility in production.
Moreover, the use of automated sealing equipment allows breweries to focus on other critical aspects of production, such as brewing and quality control. By streamlining the distribution process, breweries can allocate more resources to research and development, experimenting with new recipes and brewing techniques. This automation also enables breweries to respond quickly to market demands, allowing for rapid changes in production to meet consumer preferences. In summary, bottling and canning lines are essential tools in the brewing industry, enabling efficient and consistent sealing of beer containers, which is vital for successful distribution and sales.
Crafting Beer with a fruity Twist: Techniques for Flavorful Brews
You may want to see also
Consumer Experience: Proper sealing ensures beer freshness and taste
The art of sealing beer is an essential practice that significantly impacts the overall consumer experience, especially in the context of bars and restaurants. Proper sealing techniques are crucial to maintaining the freshness, flavor, and quality of beer, ensuring that patrons receive the best possible drinking experience. When a bar or restaurant takes the time to properly seal their beer, they are demonstrating a commitment to their customers' satisfaction and the preservation of the beverage's unique characteristics.
One of the primary benefits of proper sealing is the preservation of beer's freshness. Beer, like any other beverage, is susceptible to oxidation and exposure to air, which can lead to a rapid loss of flavor and aroma. By using appropriate sealing methods, bars can minimize the contact between the beer and air, thereby slowing down the degradation process. This ensures that the beer remains crisp, flavorful, and enjoyable from the moment it is poured until the last drop is consumed. Patrons appreciate receiving a cold, refreshing beer that tastes as good as it did when it was first brewed.
In addition to freshness, proper sealing plays a vital role in maintaining the taste and quality of beer. Beer is a complex beverage with various ingredients and flavors, and its taste can be easily altered by improper handling. Sealing techniques, such as using tamper-evident caps or specialized beer bottles with one-way valves, help to prevent contamination and maintain the beer's original character. This is particularly important for craft beers or specialty brews, where unique ingredients and brewing processes contribute to distinct flavors. By ensuring that the beer is sealed correctly, bars can guarantee that customers experience the intended taste and quality of the beverage.
For consumers, the impact of proper sealing is often subtle but significant. When a beer is properly sealed, it arrives at the table with a rich, inviting aroma and a clear, vibrant appearance. The first sip reveals a burst of flavors that were carefully preserved during the sealing process. This level of freshness and taste consistency is a testament to the bar's attention to detail and respect for the beer's natural qualities. Patrons can trust that the beer they are drinking is of high quality and has been handled with care, enhancing their overall enjoyment of the beverage.
Furthermore, proper sealing practices contribute to the overall reputation and success of a bar or restaurant. Word-of-mouth recommendations and online reviews often highlight the quality and consistency of the beer served. When customers consistently praise the freshness and taste of the beer, it reflects positively on the establishment. Bars that prioritize proper sealing techniques not only provide a better experience for their patrons but also build a loyal customer base that appreciates the attention to detail and commitment to quality.
In summary, proper sealing is a critical aspect of the consumer experience in the beer industry. It ensures that beer remains fresh, flavorful, and of high quality from the moment it is brewed to the time it is served. By implementing appropriate sealing methods, bars and restaurants can showcase their dedication to customer satisfaction and the preservation of beer's unique characteristics. This attention to detail ultimately enhances the overall drinking experience, leaving a positive impression on patrons and fostering a thriving beer culture.
Unraveling the Mystery: Does Beer Add Pounds?
You may want to see also
Frequently asked questions
Beer bottles and cans come in various shapes and sizes, each with unique characteristics. Common bottle types include the long-neck bottle, often used for premium lagers, and the stubby bottle, which is shorter and wider, typically used for craft beers. Cans come in two main varieties: the standard can, which is the most common and holds 12 ounces, and the tall can, which is taller and can hold 16 ounces or more.
Beer bottles and cans are sealed using different methods. Bottles are often closed with a twist-off cap, which is made of plastic or metal. These caps are designed to be easy to open and provide an airtight seal. Cans, on the other hand, are typically sealed with a pull-tab and a can end. The pull-tab is a small piece of paper or foil that is pulled to open the can, while the can end is a metal or plastic closure that fits over the top of the can and is sealed with a high-temperature process.
Yes, the beer industry is constantly evolving, and new sealing technologies are being introduced. One innovative method is the use of crown caps, which are made of aluminum and feature a unique crown-like design. These caps are known for their tight seal and are commonly used in premium and craft beer bottles. Another advancement is the implementation of aseptic packaging, which involves sterilizing the beer and sealing it in a sterile container, ensuring a longer shelf life and maintaining the beer's freshness.