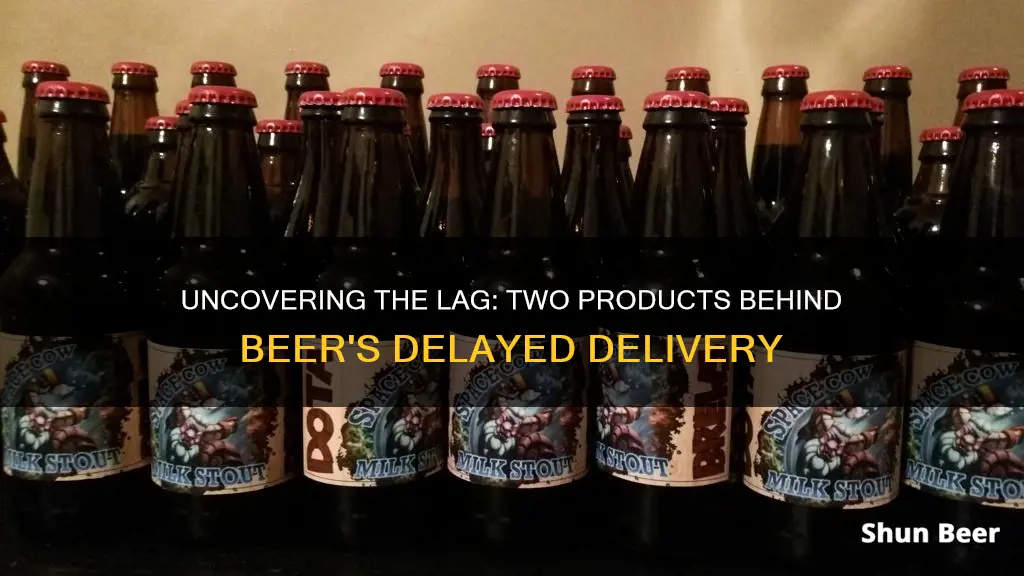
In the Beer Game, a popular supply chain management simulation, two key products often exhibit lag time, which can significantly impact the game's dynamics. These products, typically raw materials or components, have longer lead times for replenishment, causing delays in production and potential shortages. Understanding these products' characteristics and their impact on the game is crucial for players to optimize their inventory management and ensure a steady supply of finished goods.
What You'll Learn
- Inventory Management: Lag time in inventory, leading to stockouts and lost sales
- Production Planning: Delayed production, causing a backlog and missed delivery deadlines
- Supplier Reliability: Unreliable suppliers, resulting in delayed deliveries and production halts
- Transportation Logistics: Inefficient transportation, leading to delayed product arrival and increased costs
- Quality Control: Inadequate quality checks, causing defects and recalls, impacting production timelines
Inventory Management: Lag time in inventory, leading to stockouts and lost sales
The concept of lag time in inventory is a critical aspect of supply chain management, especially in industries where product demand can be unpredictable and volatile. This phenomenon occurs when there is a delay between the time a product is ordered and the moment it arrives in the warehouse or on the sales floor. In the context of the beer game, which is a popular simulation used to teach supply chain management, lag time can have significant implications for two key products: perishable goods and high-demand items.
Perishable goods, such as beer, dairy products, or fresh produce, are particularly susceptible to lag time issues. These products have a limited shelf life and can quickly become obsolete if not managed properly. For instance, if a brewery orders a batch of beer and there is a delay in transportation or storage, the product might spoil before it reaches the retail shelves. This not only results in wasted resources but also leads to stockouts, causing disappointed customers and lost sales. To mitigate this, inventory managers should implement just-in-time inventory systems, ensuring that perishable goods are ordered and delivered frequently enough to maintain freshness without incurring excessive storage costs.
On the other hand, high-demand items, such as popular beer brands or limited-edition merchandise, can also experience lag time challenges. These products often have a short window of availability and are highly sought after by consumers. If there is a delay in the supply chain, from manufacturing to distribution, these items may sell out quickly, leaving customers disappointed and potentially driving them to competitors. To address this, inventory managers should closely monitor sales trends and adjust ordering quantities accordingly. Implementing advanced forecasting techniques and collaborating with suppliers can help reduce lead times and ensure that high-demand products are always in stock.
To effectively manage lag time, inventory managers should focus on streamlining the entire supply chain process. This includes optimizing order placement and delivery routes, improving warehouse management systems, and fostering strong relationships with suppliers. By reducing the time between order placement and product availability, companies can minimize the risk of stockouts and lost sales. Additionally, implementing real-time tracking systems and using data analytics can provide valuable insights into inventory levels and demand patterns, enabling more accurate decision-making.
In conclusion, lag time in inventory can have detrimental effects on both perishable goods and high-demand items in the beer game scenario. Effective inventory management strategies, such as just-in-time systems and demand forecasting, are essential to minimize stockouts and lost sales. By understanding the unique challenges posed by different product categories, businesses can enhance their supply chain efficiency and ensure customer satisfaction.
Warsteiner: Is This German Lager a True Lager?
You may want to see also
Production Planning: Delayed production, causing a backlog and missed delivery deadlines
In the context of the Beer Game simulation, understanding and managing lag time in production planning is crucial for success. This scenario often involves two key products: beer and ingredients. The lag time in production refers to the delay between the order placement and the actual availability of the product, which can significantly impact the supply chain.
When production planning is delayed, it creates a ripple effect throughout the entire system. The primary issue arises when the demand for beer exceeds the available supply due to this lag. As a result, the company may face a backlog of orders, leading to missed delivery deadlines. This can have severe consequences, including dissatisfied customers, lost sales, and potential damage to the company's reputation.
To address this challenge, it is essential to optimize the production process and minimize lag time. Here are some strategies to consider:
- Just-in-Time (JIT) Inventory Management: Implement a JIT system to ensure that raw materials and components are delivered just before the production process begins. This reduces storage costs and minimizes the risk of excess inventory. By receiving materials just in time, you can start production promptly, reducing the overall lag.
- Efficient Scheduling: Develop a detailed production schedule that accounts for all steps, from raw material procurement to the final product's assembly. Identify potential bottlenecks and allocate resources accordingly. Efficient scheduling ensures that each stage of production is completed without unnecessary delays, thus reducing the overall lag time.
- Real-time Monitoring: Utilize technology to monitor the production process in real-time. This allows for immediate identification of any deviations from the plan. With real-time data, you can quickly address issues, such as machine breakdowns or supply shortages, and take corrective actions to minimize delays.
- Supplier Collaboration: Foster a collaborative relationship with suppliers to ensure timely delivery of raw materials. Regular communication and performance reviews can help identify potential delays and allow for proactive measures. By working together, you can optimize the supply chain and reduce the lag time associated with ingredient procurement.
By implementing these strategies, companies can effectively manage lag time in production planning, ensuring a steady supply of beer to meet customer demands. It is crucial to maintain a delicate balance between production and demand to avoid backlogs and missed deadlines, ultimately contributing to the success of the Beer Game simulation.
The Ultimate Guide to Corned Beef and Cabbage: Beer or No Beer?
You may want to see also
Supplier Reliability: Unreliable suppliers, resulting in delayed deliveries and production halts
In the context of the Beer Game, supplier reliability is a critical aspect that can significantly impact the success of a manufacturing operation. Unreliable suppliers, characterized by delayed deliveries and production halts, can disrupt the entire supply chain and lead to a cascade of issues. This scenario highlights the importance of maintaining strong relationships with suppliers and implementing robust processes to ensure timely and consistent deliveries.
One of the primary consequences of unreliable suppliers is the disruption of production schedules. When suppliers consistently fail to deliver raw materials or components on time, it directly affects the manufacturing process. This can result in production halts, where the assembly line is temporarily stopped due to a lack of essential inputs. Such disruptions can cause a ripple effect, impacting the overall efficiency and productivity of the organization. For instance, if a supplier's delayed delivery causes a production halt, it may lead to missed deadlines, dissatisfied customers, and potential financial losses.
To mitigate these issues, companies should focus on building strong supplier relationships. Regular communication and performance monitoring are essential. Establishing key performance indicators (KPIs) related to delivery times, quality, and reliability can help identify potential issues early on. By setting clear expectations and providing feedback, organizations can encourage suppliers to improve their performance and meet agreed-upon timelines. Additionally, implementing a supplier ranking system based on reliability and performance can help prioritize and manage relationships effectively.
Another strategy to enhance supplier reliability is to diversify the supplier base. Relying on a single supplier for critical components or materials can be risky. If that supplier encounters issues, it could lead to a significant lag in production. By having multiple suppliers, companies can ensure a more consistent supply of inputs, reducing the likelihood of production halts. However, it is crucial to maintain open communication and collaboration with all suppliers to ensure they are aligned with the organization's goals and expectations.
Furthermore, implementing just-in-time inventory management practices can help minimize the impact of supplier delays. This approach involves ordering and receiving materials just before they are needed in the production process. By reducing excess inventory, companies can minimize the risk of stockouts and ensure that only the required quantities are available, thus avoiding potential waste. However, this strategy requires precise coordination with suppliers to ensure timely deliveries and efficient inventory management.
In summary, supplier reliability is a critical factor in the Beer Game, as unreliable suppliers can lead to delayed deliveries and production halts. To address this, organizations should focus on building strong supplier relationships, implementing performance monitoring, diversifying the supplier base, and adopting just-in-time inventory management practices. By taking these proactive measures, companies can ensure a more stable and efficient supply chain, ultimately improving their overall performance and competitiveness in the market.
Mastering Pressure Fermentation: A Guide to Craft Beer Magic
You may want to see also
Transportation Logistics: Inefficient transportation, leading to delayed product arrival and increased costs
In the context of the Beer Game, which is a popular simulation used to teach supply chain management, the concept of lag time in transportation can significantly impact the performance of a company's logistics operations. This phenomenon occurs when there is a delay between the time a product is ordered and the moment it reaches the customer, often due to inefficiencies in the transportation process. Here's an analysis of how this can affect two key products:
Product A: Perishable Goods
Perishable goods, such as fresh produce, dairy, or certain types of packaged food, are highly susceptible to lag time in transportation. These products often have a short shelf life and must be delivered quickly to maintain their quality and freshness. For instance, consider a company specializing in organic fruit juices. If there is a delay in the transportation of these juices from the farm to the distribution center, the product may spoil, leading to increased costs and potential waste. Inefficient transportation could result in:
- Wasted Inventory: Delayed deliveries might cause the product to exceed its shelf life, rendering it unusable and leading to financial losses.
- Customer Dissatisfaction: Customers may receive expired or subpar products, damaging the company's reputation and leading to negative feedback.
- Increased Costs: To mitigate the risk of spoilage, the company might need to invest in faster transportation methods, which can be costly.
Product B: Time-Sensitive Electronics
Electronics, especially those with advanced technology and rapid obsolescence, are another example of products that suffer from lag time in transportation. Consider a tech company launching a new smartphone. Any delay in getting the devices from the manufacturing plant to the retail stores can have significant consequences:
- Missed Market Opportunities: If the product takes longer than expected to reach shelves, competitors might capitalize on the delay, gaining a larger market share.
- Price Sensitivity: Customers often expect the latest technology at competitive prices. Delays can lead to increased costs due to storage and potential price wars with competitors.
- Brand Reputation: Prolonged lag time may reflect poorly on the company's ability to deliver products promptly, potentially damaging its brand image.
To address these issues, companies should focus on optimizing their transportation logistics. This can include investing in efficient delivery networks, utilizing real-time tracking systems, and implementing dynamic inventory management to minimize the impact of lag time. Additionally, building strong relationships with transportation providers can help ensure timely deliveries and better cost management.
In the Beer Game simulation, understanding and managing lag time in transportation is crucial for achieving optimal supply chain performance. By recognizing the potential consequences for perishable goods and time-sensitive products, companies can take proactive measures to enhance their logistics operations and maintain a competitive edge in the market.
Exploring the Effects: Beer Bong Experiment Results
You may want to see also
Quality Control: Inadequate quality checks, causing defects and recalls, impacting production timelines
In the context of the beer game, which simulates the complexities of supply chain management, the concept of lag time is crucial to understanding the impact of quality control on production timelines. Lag time refers to the delay between the placement of an order and the actual delivery of the product, and it can significantly affect the overall efficiency of the production process. When it comes to quality control, inadequate checks can lead to a cascade of issues that extend beyond the immediate product defects.
One of the primary consequences of poor quality control is the increased likelihood of defects in the final product. This is especially critical in the beer game, where the quality of the product directly influences customer satisfaction and brand reputation. For instance, if a brewery fails to conduct thorough inspections during the brewing process, it may result in batches of beer with off-flavors, improper alcohol content, or even contamination. These defects can lead to immediate recalls, causing a significant lag in production timelines. The process of identifying and addressing the issue, recalling the affected products, and then re-brewing and re-inspecting them can be time-consuming and costly.
Moreover, inadequate quality checks can create a ripple effect throughout the supply chain. When defects are not caught early, they may go unnoticed until the products reach the distribution stage or even the customers. This can lead to a higher rate of returns, customer complaints, and negative reviews, all of which can damage the brand's reputation and lead to a loss of market share. In the beer game, this could translate to a decrease in sales and revenue, further exacerbating the lag time in the production cycle.
To mitigate these issues, it is essential to implement robust quality control measures at every stage of production. This includes regular and thorough inspections, both during the brewing process and after packaging. Advanced testing methods, such as sensory analysis and laboratory tests, can be employed to ensure that the beer meets the desired standards. Additionally, investing in employee training to enhance their understanding of quality control procedures can significantly reduce the likelihood of human error, which often contributes to defects and recalls.
By prioritizing quality control and addressing the root causes of defects, companies can minimize the lag time in the beer game. This, in turn, improves overall efficiency, reduces costs associated with recalls and reworks, and enhances customer satisfaction. Effective quality control is a critical aspect of supply chain management, ensuring that products meet the required standards and that the production process remains smooth and timely.
Mastering the Art of Hex Beer Nut: A Comprehensive Guide
You may want to see also
Frequently asked questions
The two products in the Beer Game that typically exhibit lag time are raw materials and finished goods. Raw materials, such as hops, malt, and yeast, have a longer lead time to procure and produce compared to finished goods like beer. This lag time is due to the complex processes involved in their cultivation, harvesting, and manufacturing.
Raw materials in the beer-making process often require specific growing conditions and time-consuming cultivation. For example, hops need several months to grow from seeds to mature plants, and malt requires a lengthy germination and malting process before it can be used for brewing. These natural processes and the time needed for quality control contribute to the lag time.
Lag time is a critical factor in the Beer Game simulation as it influences inventory levels, production planning, and customer satisfaction. With longer lag times for raw materials, breweries might need to maintain larger inventories to ensure a consistent supply, which can impact cash flow. Additionally, managing the timing of production and delivery becomes essential to meet customer demand without excess inventory.
While finished goods like beer are ready for distribution and sale, they still have some lag time associated with them. This is primarily due to the time required for brewing, fermentation, and packaging processes. The lead time for these processes varies depending on the brewing method, batch size, and desired quality standards.
To minimize lag time, breweries can implement various strategies. These include just-in-time inventory management, where they order raw materials and ingredients as needed, reducing storage costs and waste. Additionally, optimizing production schedules, investing in faster brewing technologies, and maintaining strong supplier relationships can help reduce the overall lag time in the Beer Game simulation.